Despite the adverse market conditions remarable growth
“Our Vision 2050 and Mission Blue initiatives are without a doubt the right forward-looking strategies for Schubert. We have defied the trend and achieved a very good annual result. It’s a team effort we can be proud of,” summarises Marcel Kiessling, Managing Director Sales and Service at Gerhard Schubert GmbH. Schubert is clearly maintaining its leading role in the packaging industry – with steady growth for the thirteenth year in a row, even under very difficult market conditions. The Schubert Group has also continued its growth trend with an estimated overall performance of 400 million euros. The Group now has around 1,700 employees, of whom some 1,200 work for Gerhard Schubert GmbH in Crailsheim. Despite a shortage of skilled labour, the company succeeded in increasing its core workforce and, with the help of increased productivity, successfully processed 2023’s high order volume. Production and assembly capacities have also been fully utilised so far this year and the order books are full until 2025. This is an extremely favourable starting position for innovative product developments, especially as the budget for research and development in 2024 is once again the largest single budget, representing nine per cent of overall performance.
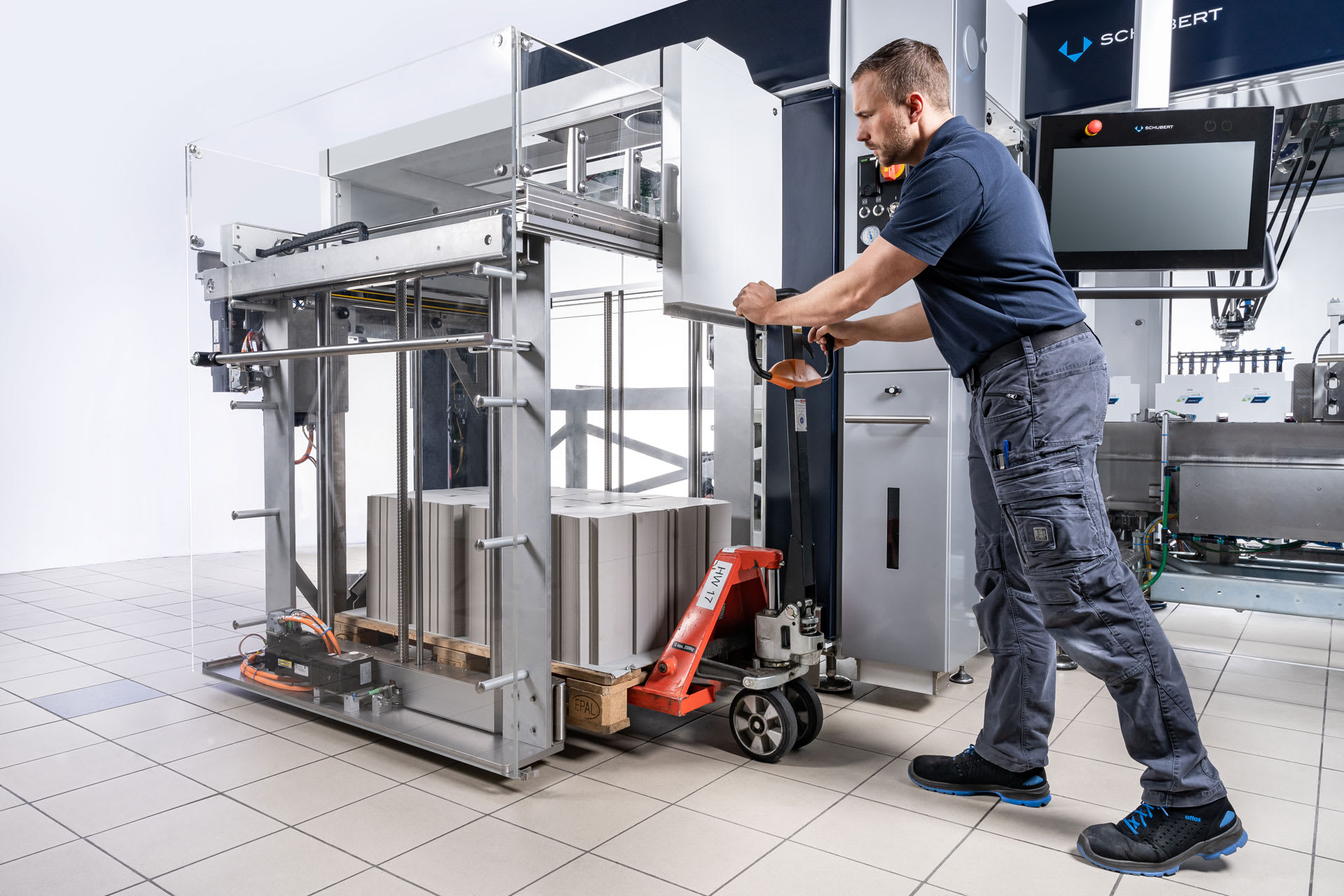
Key future technologies include the resource-saving TLM Comfort Feeder in conjunction with the A3 carton erector for feeding cardboard blanks.
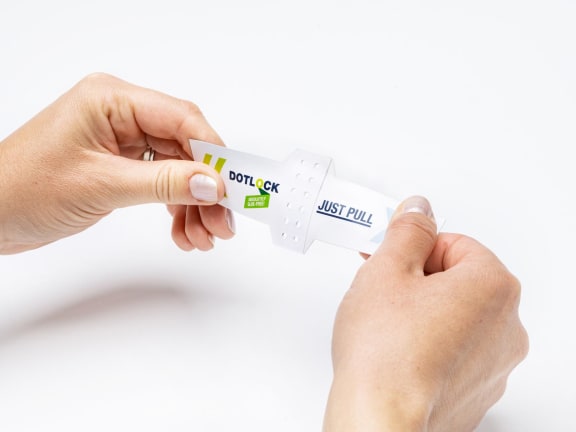
One of the new Schubert technologies for sustainable packaging solutions is Dotlock which enables the creation of strong joints for cardboard packaging without the need for hot glue.
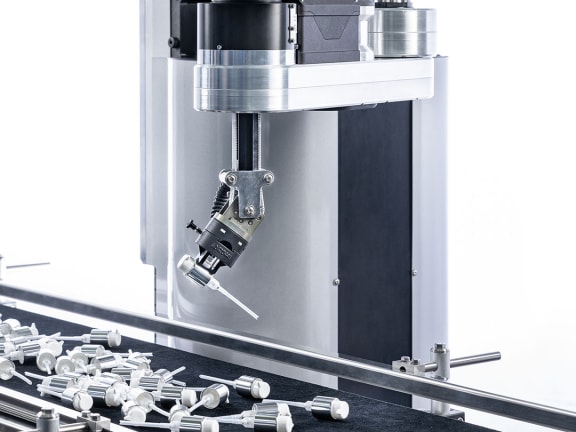
The tog.519 collaborative robot automates feeding at the packaging machine and is ready for series production.
High vertical integration, increased capacities
Another decisive advantage for Schubert is its high in-house production rate of 53 per cent. Peter Gabriel, Managing Director Finance and Supply Chain, adds: “With Schubert Fertigungstechnik GmbH, which produces mechanical components and assemblies made of aluminium or using the 3D printing process, and Schubert System Elektronik GmbH, which develops and supplies electronic components, we are covering important areas of our production in-house – and making them less dependent on global supply chains.” At the same time, the manufacturer benefits from short transport routes, as both subsidiaries are also located in Baden-Württemberg. On average, some 140 packaging machines are built and delivered every year at the main site in Crailsheim – almost two thirds of these are for the food industry alone (39 per cent) and the confectionery industry (25 per cent). A further 17 per cent go to manufacturers of pet food. Schubert machines are also used to pack beverages, cosmetics, cleaning agents and pharmaceutical products.
An all-new assembly hall and office complex were built Schubert’s headquarters
With the completion of the new assembly hall and office complex at the main site, Schubert has once again significantly expanded its production capacity. On a total area of 13,000 square metres, 30 per cent more space has been created for final assembly, as well as workspaces for 300 employees. The design and assembly areas are now located even more closely together, which fosters direct feedback, creative technological advances and the ongoing development of energy-saving machine components. The state-of-the-art working environment also supports the company’s long-term goal of becoming one of Germany’s best employers and therefore attracting sufficient skilled labour in the long term. The new buildings’ energy concept also has a positive impact on sustainability: Equipped with one of the largest ice storage systems in the world, heat pump technology and photovoltaics on the roof, the buildings are operated 100% climate-neutrally in accordance with Scope 1 and 2 of the Greenhouse Gas Protocol. “With our Mission Blue Sustainability Initiative, we have set ourselves very ambitious environmental protection targets. We are delighted that we have come a step closer to achieving these goals with the new buildings,” reports Gerald Schubert, Shareholder of the Schubert Group and Managing Director of Schubert Business Development GmbH.
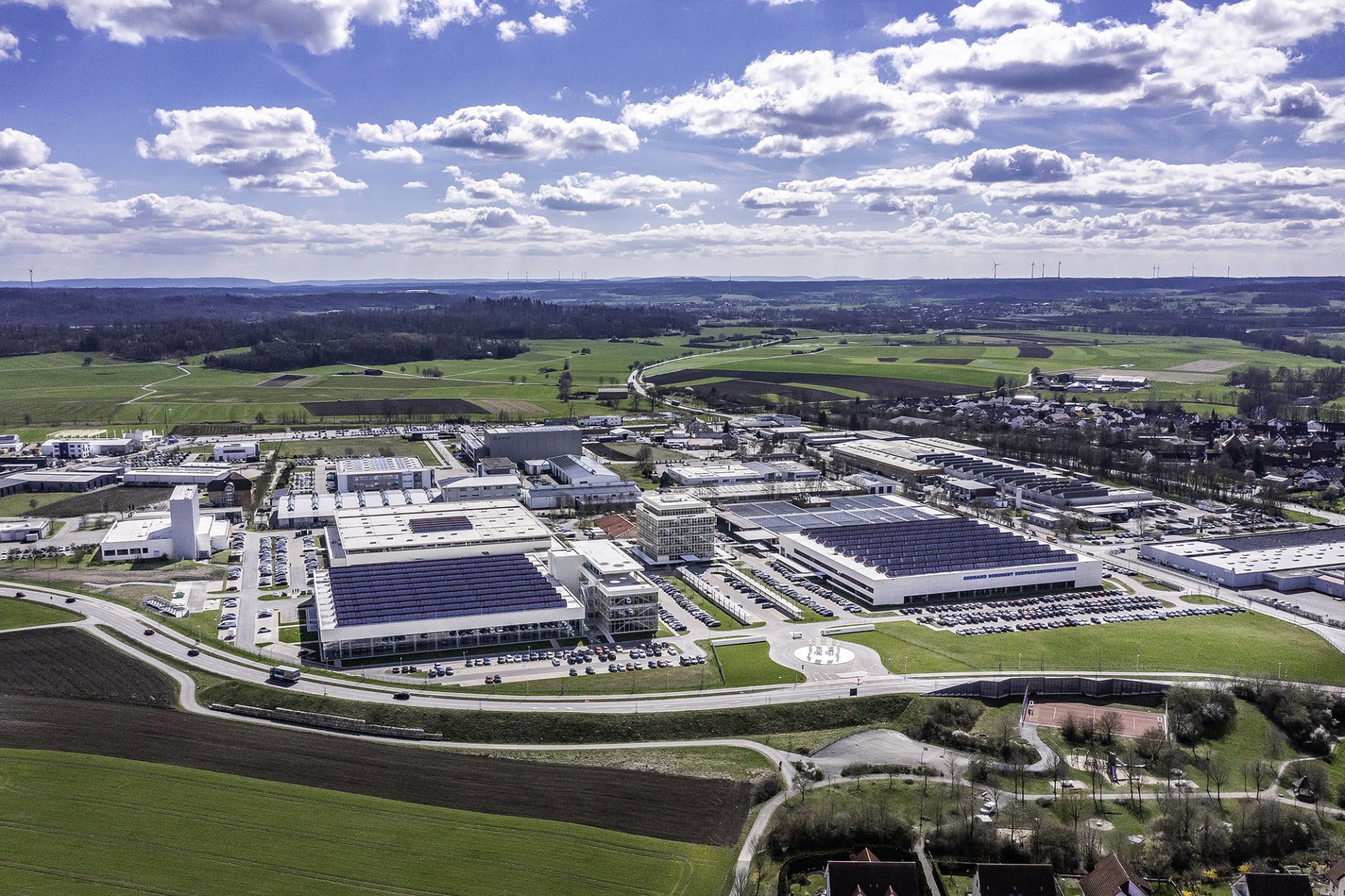
Schubert has once again significantly expanded its production capacities with the construction of a new assembly hall and office building at its main site in Crailsheim, Germany.
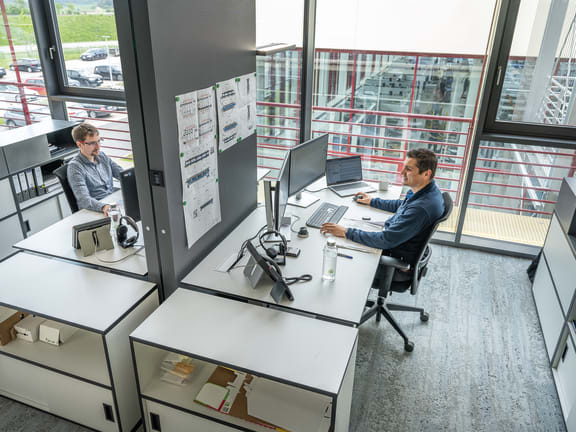
The design and assembly areas are now even closer together, which fosters direct feedback and encourages the development of creative technological advances.
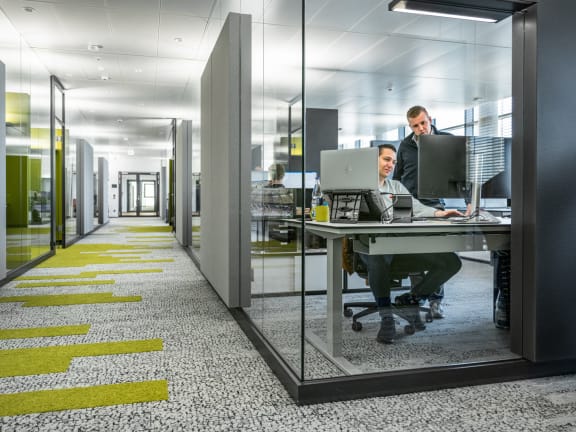
The state-of-the-art working environment supports Schubert’s long-term corporate goal of being one of Germany’s best employers.